A new version of The London Plan has recently been published. Here, Henry Bareham – Director of New Build for Alumasc Roofing Systems – outlines how Alumasc’s roofing solutions provide designers with the tools to comply with key requirements of the London Plan 2018.
Introduction to The London Plan 2018
The latest version of the plan includes policies to address three areas of focus for a more sustainable built environment in our capital city:
1. Policy G5 – Urban Greening
2. Policy S14 – Managing Heat Risk
3. Policy SI13 – Sustainable Drainage – applicable to Blue Roofs
1. Policy G5 Urban Greening
Policy G5 seeks to increase the amount of green space in the Greater London region. Green space has been proven to have significant health and wellbeing benefits in addition to environmental improvements.
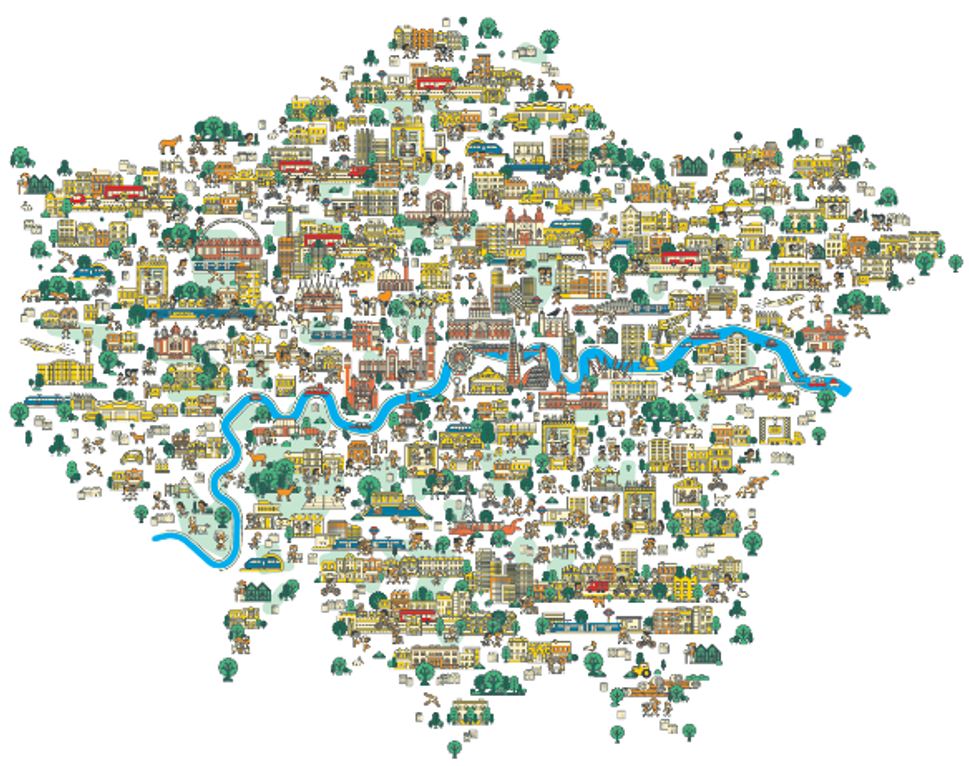
Policy G5 requires that major development proposals “contribute to the greening of London by including urban greening as a fundamental element of site and building design, and by incorporating measures such as high-quality landscaping (including trees), green roofs, green walls and nature-based sustainable drainage.”
The Plan outlines how Boroughs should identify the amount of urban greening that is required. An Urban Greening Factor (UGF) is to be specified for each new development. The UGF will vary, but the Mayor has recommended target scores of 0.3 for commercial developments and 0.4 for residential developments.
2. Policy S14 Managing Heat Risk
Policy S14 seeks to reduce the need for air conditioning in buildings and to minimise the health risks caused by the urban heat island effect (UHIE).
Major developments will need to include energy strategy proposals that reduce the potential for overheating and reliance on air conditioning systems. Policy S4 sets out a hierarchy of measures that should be considered to achieve compliance with this requirement:
1. Energy efficient design of the building to minimise internal heat generation; and
2. Use of building orientation, shading, albedo, fenestration, insulation and green roofs to reduce the amount of heat entering the building.
3. Policy SI13 Sustainable Drainage – applicable to Blue Roofs
As in many urban areas, the replacement of previous surfaces with hard landscaping has increased the burden on urban drainage systems in the capital. Policy SI13 requires Lead Local Flood Authorities to operate Local Flood Risk Management Strategies and Surface Water Management Plans that identify areas of particular surface water management risks and set out strategies to reduce these risks.
The Policy requires that development proposals aim to achieve greenfield run-off rates and manage surface water run-off as close to its source as possible. Policy SI13 also sets out a hierarchy of solutions to achieve these requirements:
1. rainwater harvesting (including a combination of green and blue roofs)
2. infiltration techniques and green roofs
3. rainwater attenuation in open water features for gradual release
4. rainwater discharge direct to a watercourse (unless not appropriate)
Tried and Tested single-source solutions for the London Plan 2018
It is clear that whilst each policy addresses specific design issues, many of these problems are inter-related. The introduction of urban greening into the capital will not only provide the health and wellbeing, amenity and environmental benefits that are sought after in Policy G5. Urban greening is also cited as one of the preferred solutions to manage heat and stormwater management risks.
There are a number of ways that urban greening can be introduced into our capital city. However, in view of the scarce availability of landscape at ground level in city spaces, one of the key areas of focus for the introduction of vegetation has been the use of roof spaces for the inclusion of green or blue roofs.
Blackdown Green Roofs
Whilst many of the installed green roofs are often out of common sight, there are a growing number of green roofs in the Greater London area. Alumasc Roofing Systems have been providing green roof solutions in the capital for over 25 years and its specialist green roof division – Blackdown – has nearly 20 years of experience. One of the most visible examples of this is at the West Ham bus station, which remains one of the largest green roofs installed in the UK to date. Indeed, it is thought that this installation inspired the more recent incorporation of a green roof at a bus station in Chester, see here.
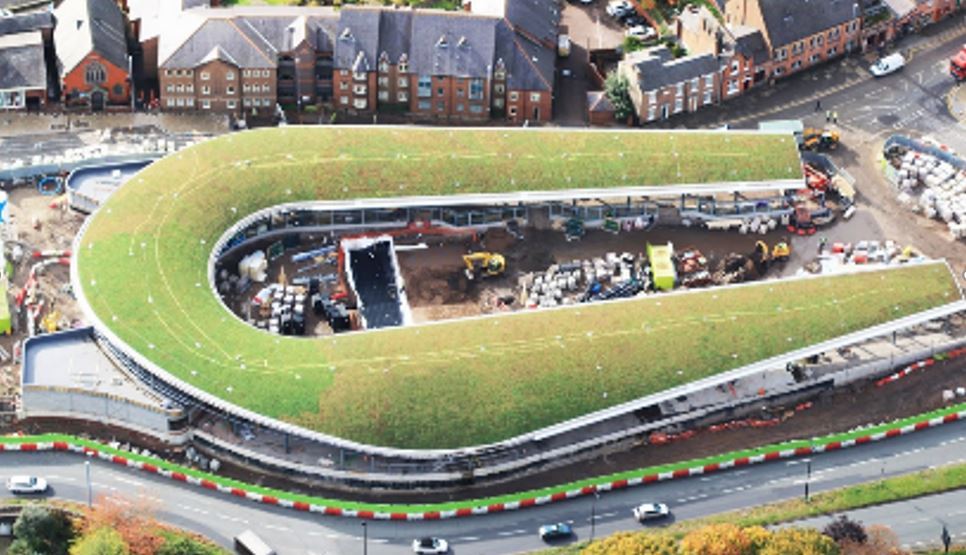
Alumasc recognises that there are numerous different drivers for green roof specifications. Alumasc’s technical team engages with designers and installers at each stage of the project lifecycle to ensure that the system design and installation are tailored to achieve the specific design objectives. Our experts are involved from pre-planning stage right through the installation phase and to project completion.
It is this early involvement that ultimately led to the development of Alumasc’s BluRoof solution nearly 5 years ago.
Alumasc BluRoof
Alumasc’s patented BluRoof system allows for stormwater to be detained at roof level and released gradually to reduce potentially flood-inducing peak rates of runoff whilst also regenerating its capacity ahead of any subsequent storm event. Alumasc Technical Services provide design calculations as part of its support package for BluRoof specifications.
The BluRoof system has been carefully designed to account for all of the risks associated with stormwater attenuation at roof level. Paramount in this is the single source nature of the solution – Alumasc’s BluRoof system comprises proven waterproofing solutions, insulation, outlets and green roof components all supplied by Alumasc as part of a quality-controlled system. This single source warranted solution is compatible with the requirements of key industry stakeholders, such as the NHBC and LABC. Alumasc clients also value the benefit of a single source BluRoof warranty. This exploits the combined expertise of Alumasc’s Roofing Division and Harmer Engineered Drainage Systems; allowing a truly single source solution that we believe is integral to a system of this nature.
BluRoof system specifications are built upon the Derbigum or Hydrotech waterproofing solutions that (a) have proven ‘durability beyond the laboratory’ performance records and (b) are supported by BBA certification for ‘completely flat roof’ designs. Both aspects are fundamental to successful blue roof strategies:
• Hydrotech Hot Melt boasts the longest track record of any Hot melt on the marketplace – spanning over 53 years. Over this time, over 180 million square metres have been installed without a single product failure!
• Derbigum high-performance bituminous membranes also offer a similarly impressive track record.
The product has been used for over 40 years – again without a product failure – and has been accredited by the BBA as having a life expectancy of 40+ years.
Alumasc’s BluRoof system has been specified at a host of sites across the UK and is undoubtedly now seen as an excellent option to provide relatively low cost sustainable drainage capacity as part of a broader Surface Water Management Plan. BluRoof case studies are presented on our website, including installations at Kew Bridge Phase 2 and North West Cambridge.
If you have any requirements for waterproofing, green roofs or BluRoof please feel free to contact Henry to discuss your requirement further.
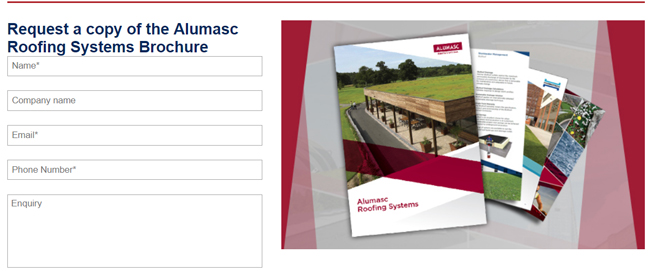