When it comes to large-scale new build projects it is essential that the choice of structural waterproofing is of the highest standard and installed with the greatest of expertise and on-site support to ensure the longevity and risk-free future of the building.
There are various ways in which the waterproofing can be installed in order to provide long-term peace of mind. Hydrotech is the premier hot melt system for high performance green roofs, podiums and highly detailed waterproofing schemes and has been used world-wide for over 50 years, with an astonishing record of zero product failures.
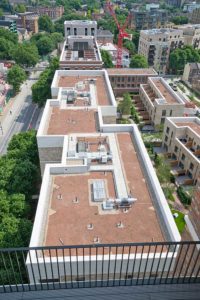
Elephant and Castle, London
Alumasc provide full bespoke design collateral and documentation based around your project and provide a full understanding and solution to any potential areas that need specific attention such as deck deflection and drainage issues, after all, every project is different. Working with our comprehensive technical team during this process ensures that all areas are covered – this is The Alumasc Promise.
What is the Alumasc Promise Service Offer?
Only fully carded, Hydrotech Registered Contractors install our hot melt systems and receive full training under controlled Alumasc training facilities.
Alumasc’s team of site technicians will support you through your project by regularly visiting and inspecting site to ensure all work(s) are carried out to the highest standards. On completion of installation and testing we issue a detailed handover package as proof we have delivered on our Promise. This package includes the project specification, test data, site reports and maintenance schedules. This also includes a full Alumasc backed warranty covering aspects such as product, workmanship and design – giving you full peace of mind, we also return to site every 5 years to inspect and report on the completed area.
What if a failure occurs with no warranty or insurance backed guarantee?

Kew Bridge, London
In many cases designers and contractors can be under increasing budget pressure therefore structures may end up with basic commodity systems that are not installed to adequate standards or backed up with the various ongoing support and warranties.
This is a high-risk approach as the integrity of the structure can be put under increasing pressure if the structure is not soundly waterproofed, resulting in highly costly repairs and processes in the long term.
Mark Golder – Alumasc Roofing Systems Commercial Director: “Taking care to assess and select a complete package tailored to your project allows you to be safe in the knowledge that your investment will be paid many times over”
If the structural waterproofing is not installed to a high quality some of the potential risks that can occur include interior superficial damage and staining/mould, possibly affecting services such as lighting.
Dependent on the level of water entry, repair costs could be high if there is consequential damage. The cost of exposing the membrane would be significant as inverted systems are always buried under a hard or soft landscaped area.
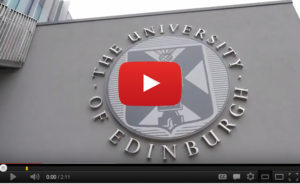
DRONE FOOTAGE: Hydrotech Structural Waterproofing Installation at the Scottish Centre for Regenerative Medicine (SCRM)
As well as the added cost of recover and repair, the damage can also make the space below temporarily unusable or damp, for example, an office building, hospital or inhabited area – this would prove to be even more costly to the installer.
Again, the quality of workmanship will prevent these issues, however the use of Alumasc’s registered operatives will also provide warranties of up to 35 years for added peace of mind. This will also include repair cover if for any reason a system was to fail. It is due to the high levels of training all Hydrotech operatives receive which has helped Hydrotech achieve the incredible zero failures in 50 years record – along with the quality of the product itself.
Quote from St James Homes London: “St James have been incorporating Alumasc’s Hydrotech system since 2009 and from this time St James are not aware of a single roofing issue relating to system failure in material or contractor labour. The level of service that Alumasc Roofing Systems provides in design, system installation and after service has proved to offer significant savings to our business in reduction of dilapidation costs. Thus, Alumasc demonstrate that whilst the Hydrotech system is not the cheapest, it does provide significant long term value”
The Promise from Alumasc
Promise is a service offer that guarantees the integrity of your roof prior to, during and after installation and is designed to safeguard you against the most common pitfalls. It gives you the security of expert installers, continual on-site supervision, professional testing and comprehensive, post-installation support.
As mentioned above, our clients find that our Alumasc Promise package provides peace of mind for the future along with an unrivalled track record of zero product failures in over 50 years – so why consider anything else?
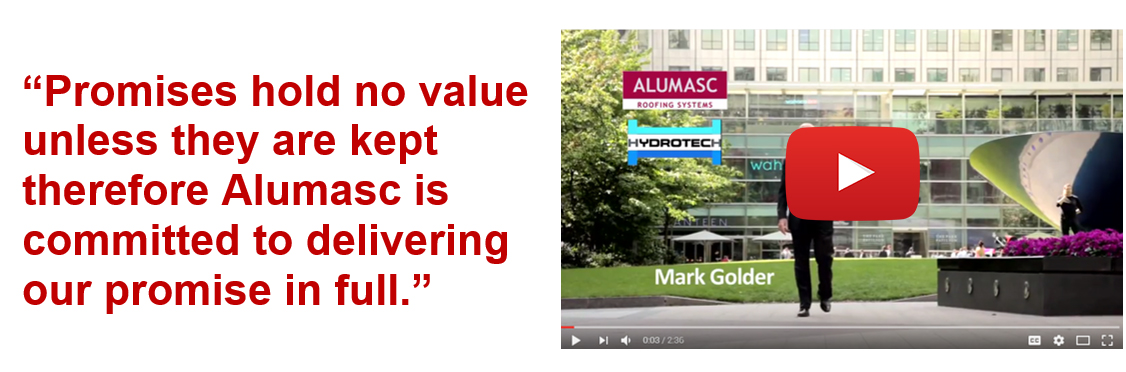
Over the years Hydrotech has been utilised on various large scale projects ranging from Canary Wharf back in 1998 and the Cheese Grater in 2014 through to the more recent/current major residential and business district developments within Nine Elms on the South Bank of the Thames, London.
“Our Promise provides Clients, Developers and Contractors with complete confidence and long-term peace of mind in the Roofing system specified on their project”
For further product information about Alumasc’s Hydrotech Structural Waterproofing click here or call our technical team on 03335 771 500.
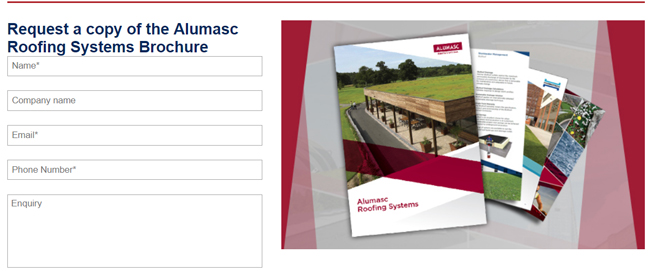